The predominant goal of FSMA 204 is to more quickly identify and remove potentially contaminated food from the market. Companies that manufacture, process, pack, or hold foods on the Food Traceability List (FTL) are required to capture, maintain, and share traceability records containing Key Data Elements (KDEs) associated with specific Critical Tracking Events (CTEs). They must provide that information, in the form of an Electronic Sortable Spreadsheet, to FDA within 24 hours of a request from the agency or within a reasonable time to which the FDA has agreed.
Andy Kennedy of New Era Partners and co-writer of FSMA 204 has designed a timeline outlining the path to compliance.
This timeline is broken into four phases:
- Learn about the rule;
- Plan your path to compliance;
- Do all the work you set out to do; and
- Review and update your processes as needed.
At this point, larger enterprises -- retailers, foodservice operators, distributors, and large processors with large supplier networks – should have completed the learning and planning phases and be poised to “do” the work.
Learn
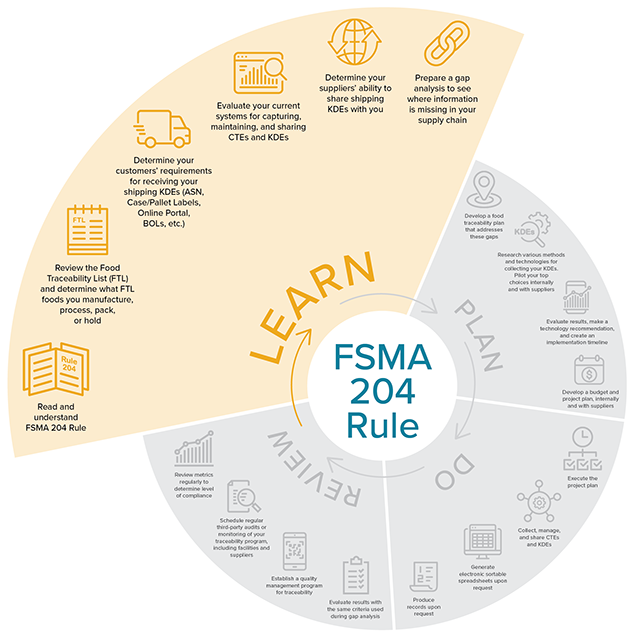
- The first step is to read and understand FSMA 204. Since the release of the rule, additional information has been published on the FDA FSMA 204 Website, including additional Traceability Lot Code information and many updates to the FAQs.
- FDA also recently posted its first video in an educational series focused on tech-enabled food traceability.
- Determine if the rule applies to you by reviewing the FTL. You’ll be subject to requirements if you manufacture, process, pack, or hold any foods on the FTL.
- Determine your store or restaurants' requirements for receiving your KDEs. Will they require an Advanced Shipping Notice (ASN), specific labels for cases and pallets, or ask you to enter data into an online portal?
- Determine your supplier’s ability to share shipping KDEs with you. Ensure they are sending you the data you need in a format that your systems can quickly ingest. It may make sense to implement a network traceability solution across your supply chain network, such as iFoodDS’ Trace Exchange™.
- Evaluate your current systems for capturing, maintaining, and sharing KDEs and CTEs. Prepare a detailed gap analysis to outline whether your current processes and systems enable you and your supply chain partners to fully comply with FSMA 204.
Plan
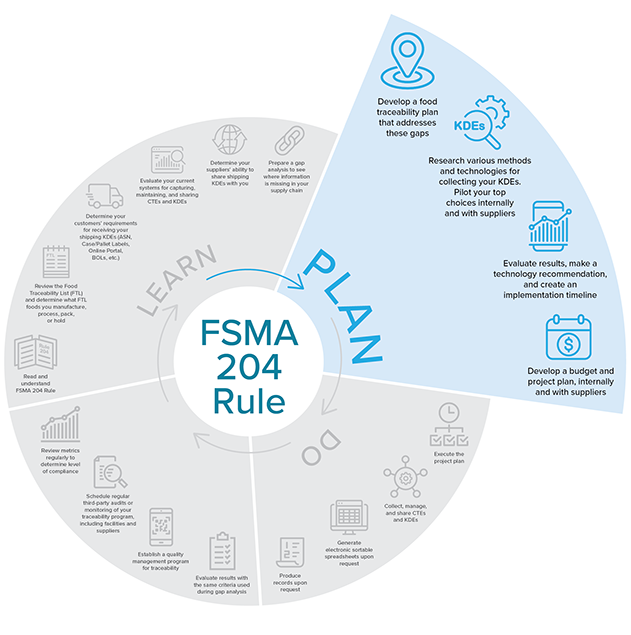
- FDA requires a Food Traceability Plan with specific requirements as to what you need to include. First, be sure to address the gaps in your systems and processes that you identified earlier.
- Research various methods and technologies for collecting your KDEs. Pilot your top choices internally and with suppliers.
- Evaluate results, make a technology recommendation, and create a traceability implementation timeline.
- Develop a budget and project plan internally and with suppliers.
Do
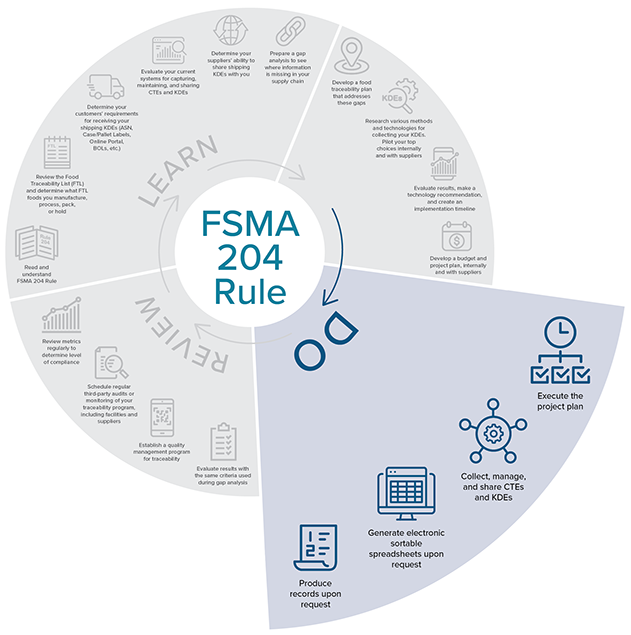
-
Execute the project plan that addresses how you plan to comply with FSMA 204 and fill any gaps you discovered in the learning and planning phases.
- Communicate with trading partners.
- Communicate internally.
- Implement your new solution. A smooth implementation process, including proper training, will set you up for success. Ensure that your new solution provider has met your requirements. Document your processes and training procedures for easy onboarding.
- Collect, manage, and share CTEs and KDEs. Start consistently collecting KDEs from suppliers, store and manage those KDEs in your internal systems, and share them with your stores or restaurants.
- Generate Electronic Sortable spreadsheets. We recommend going through the process of creating your Electronic Sortable Spreadsheet now and identifying more than one person who can do this.
- Produce records. Double-check that you have all necessary records supporting the information in the Electronic Sortable Spreadsheet. FDA may ask for these additional details after the 24-hour period.
Challenges and Roadblocks
-
Are you struggling to get your suppliers to send FSMA 204 KDEs to you?
- There is no one-size-fits-all when it comes to managing your network of suppliers, and you both may need to adjust your processes to find a method that works for everyone involved.
-
Are you struggling to find a solution that meets the unique needs of your organization, or to implement the one you’ve already chosen?
- Food Industry Association (FMI) recently put out a FSMA 204 Implementation Guide you may want to check out.
-
Are you unsure about the Electronic Sortable Spreadsheet?
- Read this guide from New Era Partners or check out these examples on the Produce Traceability Initiative web site.
-
Are you worried about how you will provide records to FDA in 24 hours and who can quickly access that information?
- FDA will tailor the information request as much as possible so you can focus your efforts on the most relevant information.
- You should have more than one person trained to access the requested information and have a trusted digital solution in place that will enable you to quickly access the information and export it into an Electronic Sortable Spreadsheet.
Review

- Once your new processes and systems have been executed, review those gaps you identified earlier.
- Establish a quality management program to measure accuracy, capture errors, and create corrective actions.
- Schedule regular third-party audits or monitoring of your traceability program to ensure that you continue to meet the FSMA 204 requirements.
- Review metrics regularly to determine the level of compliance and help you recognize gaps or areas where you need to adjust processes.
Resources Are Available
Wherever you are in your journey to FSMA 204 compliance, we are here to help.
The iFoodDS Trace Exchange solution is designed to help you easily and securely capture, store, share, and monitor KDEs, and provide the reports you need. Request a consultation to learn how we can help guide your organization.
We also recommend expert support from consultants like New Era Partners, who will provide audit tools and other services aimed at guiding your unique organization.